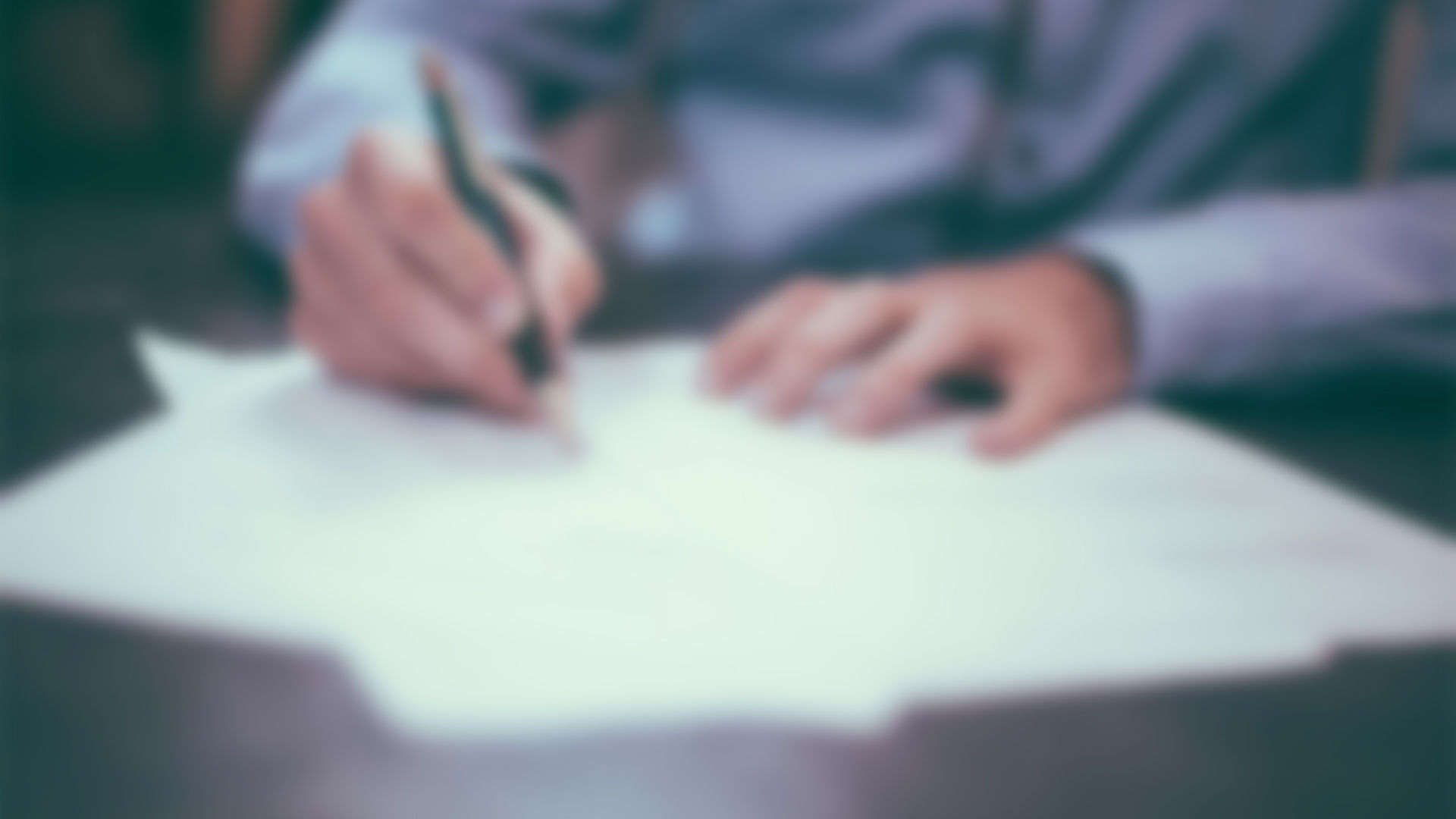
Create Your First Project
Start adding your projects to your portfolio. Click on "Manage Projects" to get started
Viscoelastic Material Testing Device
Project Type
School Project
Date
August 2023
Role
Mechanical and Electrical Designer
Objective
Design a testing device for characterizing the damping coefficient of viscoelastic damping compounds or similar products directed at vibration damping and isolation. Project guidelines required:
- Two different sensor types
- Minimum of three total sensors
- Uncertainty Analysis
SolidWorks
I led the design of the testing device for my group. The test setup was designed using Solidworks CAD. The primary concerns of the design were affordability and ease of manufacturabilty. The parts utilized were expensive if purchased new, but the vast majority of the components were repurposed from other projects trash and the measurement equipment was already available in the lab.
LabVIEW Data Collection and Generation
The NI myRIO 1900 was utilized for data collection/generation. To conduct the experiment, a sine wave is generated by the myRIO and output from a standard auxiliary audio port. The audio output is sent to a generic class D speaker amplifier. The amplifier includes a low pass to filter out high frequency noise, >400 Hz, and drives a vibration generator. Data is collected by three sensors connected to the analog inputs of the device. The three sensors are two accelerometers and one proximity sensor. The accelerometers are PCB Piezotronics 352A21 and the proximity sensor is the QRE1113 reflective optical sensor. The accelerometers are utilized to measure the intensity of vibration in the device on opposite sides of a sandwiched viscoelastic damping material. The QRE1113 sensor outputs a sine wave with varying intensity. The LabVIEW code receives the sine wave and measures outputs the frequency. This frequency is used to validate the signal generated by the myRIO.
Results and Failure Analysis
Unfortunately, the results were unsatisfactory for our objective. We failed to obtain usable information about the damping materials. Testing was hindered by issues with the amplitude measurements and the accelerometers caused numerous issues that required extensive troubleshooting that limited the time allowed for data collection. Future work could be completed to include different accelerometers such as the ADXL345 or ADXL337 to see if the results were more useful. Otherwise, a complete redesign of the test setup would be required to better explore the performance of damping materials.