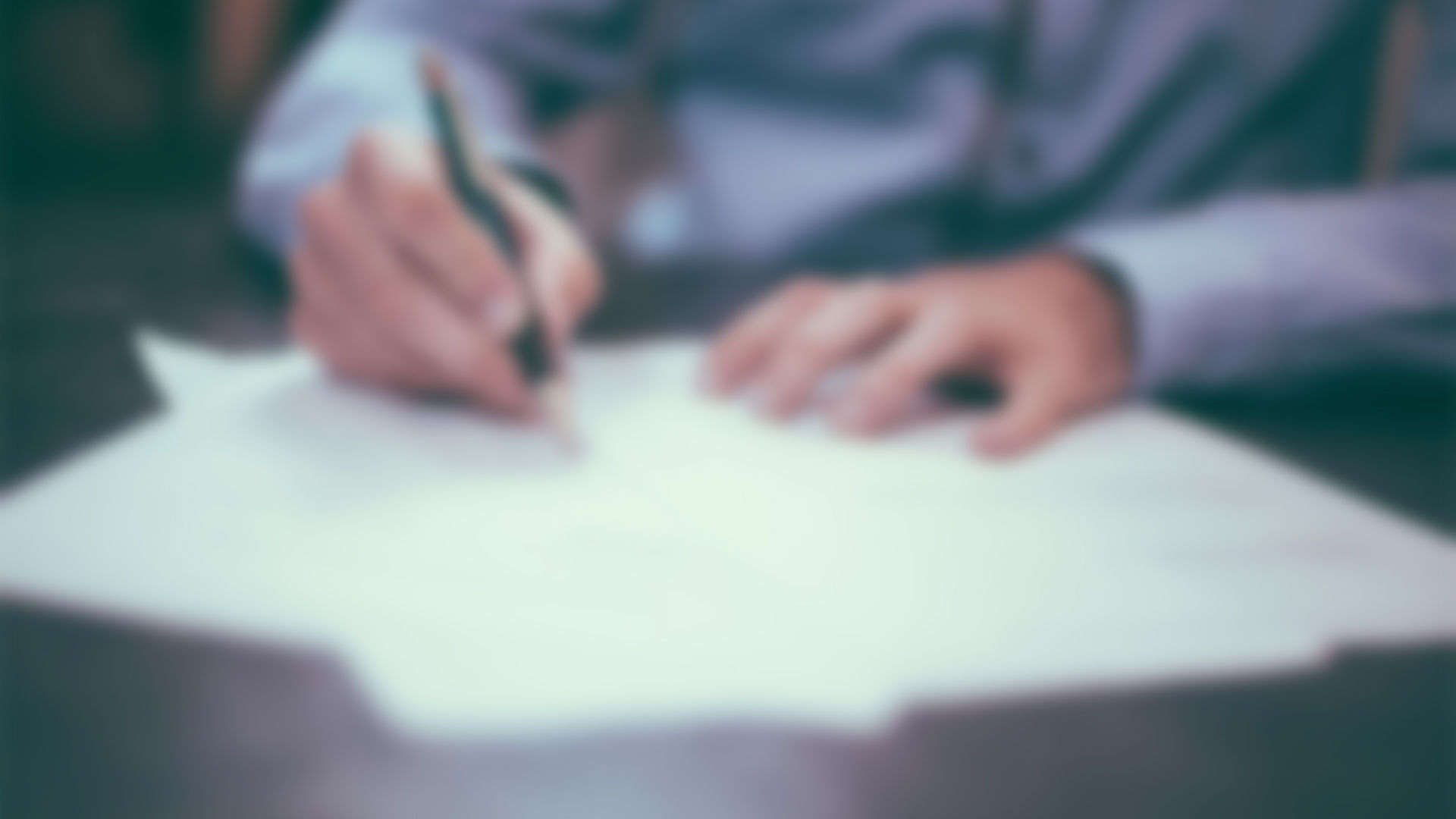
Create Your First Project
Start adding your projects to your portfolio. Click on "Manage Projects" to get started
BiSCUT (Biaxial Stretching Cadaveric Ulnar Tissue) Device
School Project
Produced for Dr. Mark Miller and the Laboratory for the Study of Mechanics in the Human Body
Date
August 2023
Role
Mechanical Design Engineer, Budgeter, Fabricator
Senior Design CAPSTONE Project
Objective
To create a device that stretches, magnifies, levitates and hydrates a cadaveric tissue sample during observation.
Fabricator
As one of the fabricators, I worked with my colleague Michael Macdonough to build all of the designs that the group created in SolidWorks. This included using Prusa FDM, Markforged, and FormLabs SLA printers. As well, I completed all of the CNC laser cutting of the acrylic base and a few laser cut stainless steel components.
Budgeter
In my role as the budgeter for the group, I handled all of the purchasing, budget updates and forecasting, and some cost analysis of the initial designs. The cost analysis was particularly interesting since our labor was free and fabrication commonly used tools that were exorbitantly expensive. As such, there was a large discrepancy between the cost of the device as purchased versus the expected cost when using outside vendors, in which a budget twelve times higher would be required
Levitation and Hydration
I would like to focus on the levitation and hydration portion of the design since I was the lead designer of this system. Initial prototypes utilized an "air hockey" approach to levitate and hydrate the tissue sample. Issues with the flow profile of these devices lead us to pursue other methods to produce smoother and more uniform flow.
The solution I landed on was the use of "Gyroid" infill as the filter material to create a smooth and constant flow profile emerging from the surface. Gyroid infill is a standard infill type provided in most 3d printer slicer software and happened to be the first type that I investigated.
Further iterations improved the performance of the device for flotation through changes made to the seals, filter material size, filter material density. As well, numerous changes were made to improve the ergonomics and sustainability of the device. Design changes in the final component reduced the amount of plastic needed by ~45%.